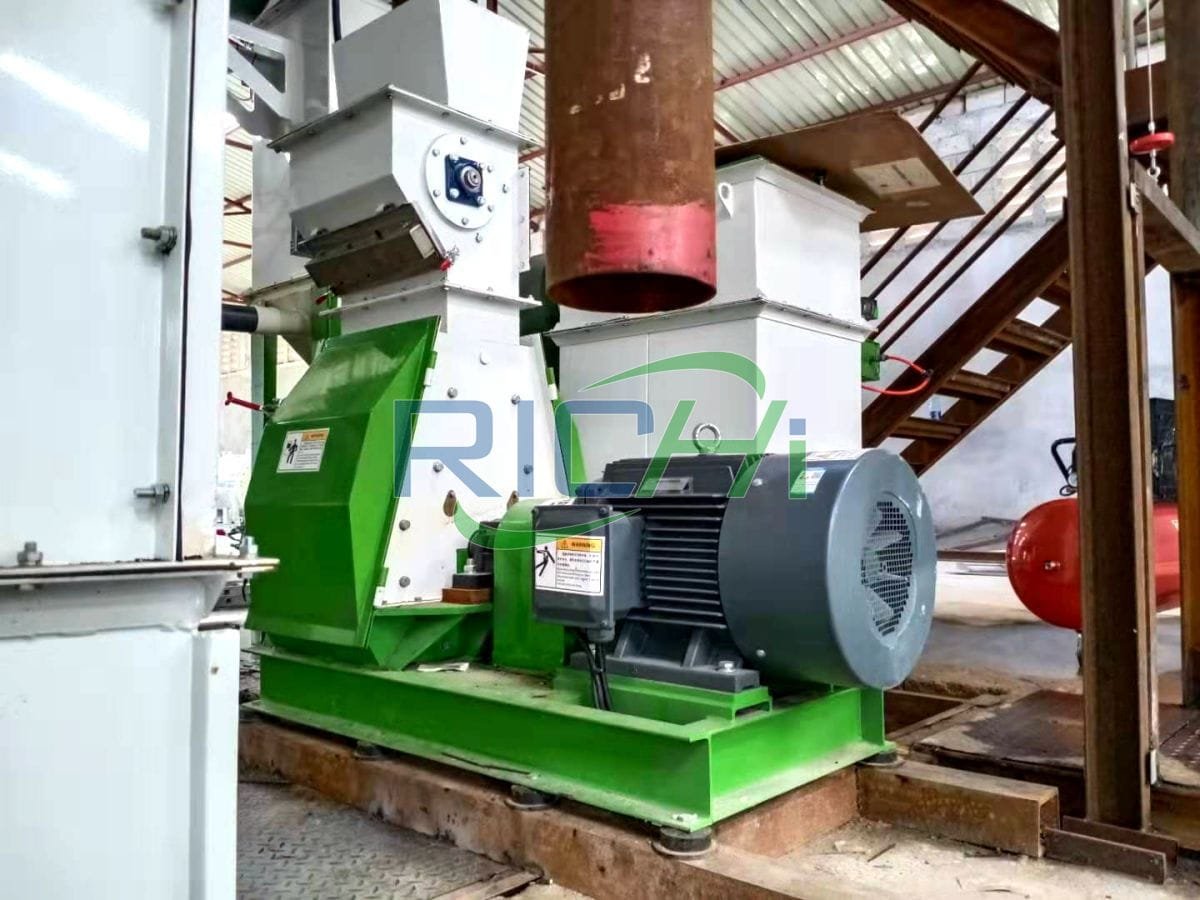
Wood pellet hammer mills are essential equipment in the biomass processing industry, used to grind raw materials into fine particles suitable for pellet production. These mills come in two main power variants: electric and diesel. While both types serve the same primary function, there are significant differences between them, with electric hammer mills often proving to be the superior choice. This article explores the distinctions between electric and diesel wood pellet hammer mills and argues why electric models are generally better.
Power Source and Efficiency
The most obvious difference between these two types of hammer mills is their power source:
- Electric Hammer Mills:
- Powered by electricity through an electric motor
- Generally more energy-efficient
- Consistent power output
- Diesel Hammer Mills:
- Powered by a diesel engine
- Less energy-efficient due to combustion losses
- Power output can fluctuate based on engine conditions
Electric hammer mills, like those offered by Biopellet Machine, typically have higher energy efficiency. They convert a larger percentage of input energy into mechanical work, resulting in lower operational costs over time.Operational CostsIn terms of ongoing operational expenses:
- Electric Hammer Mills:
- Lower fuel costs in most regions due to cheaper electricity rates
- Reduced maintenance requirements
- No need for fuel storage or handling
- Diesel Hammer Mills:
- Higher fuel costs due to diesel prices
- More frequent maintenance due to engine complexity
- Requires fuel storage and handling facilities
The electric wood hammer mill from Biopellet Machine, for instance, offers high efficiency with lower operational costs compared to its diesel counterparts. (Related post:pallet crusher)
Environmental Impact
Environmental considerations are increasingly important:
- Electric Hammer Mills:
- Zero direct emissions
- Potential for zero emissions if powered by renewable energy
- Quieter operation, reducing noise pollution
- Diesel Hammer Mills:
- Produce emissions, including CO2 and particulates
- Contribute to air pollution
- Noisier operation
Electric models are clearly superior in terms of environmental impact, aligning with growing sustainability concerns in the industry.
Maintenance and Reliability
Maintenance requirements differ significantly:
- Electric Hammer Mills:
- Fewer moving parts, leading to less wear and tear
- Lower maintenance frequency and costs
- Higher reliability and longer lifespan
- Diesel Hammer Mills:
- Complex engine systems requiring regular maintenance
- Higher risk of breakdowns due to more components
- Shorter overall lifespan due to engine wear
The simpler design of electric hammer mills, like those in the CF series from Biopellet Machine, results in more reliable operation and reduced downtime.
Performance and Consistency
In terms of performance:
- Electric Hammer Mills:
- Consistent power output leading to uniform particle size
- Instant start-up and shut-down capabilities
- Better control over grinding speed and fineness
- Diesel Hammer Mills:
- Power output can vary with engine temperature and conditions
- Require warm-up time and cool-down periods
- Less precise control over grinding parameters
The consistent performance of electric models ensures a more uniform end product, which is crucial for high-quality pellet production.
Versatility and Adaptability
Considering adaptability to different environments:
- Electric Hammer Mills:
- Suitable for indoor and outdoor use
- Can be easily integrated into automated systems
- Adaptable to various power supply configurations
- Diesel Hammer Mills:
- Primarily suited for outdoor or well-ventilated areas due to emissions
- Less compatible with automated systems
- Limited by fuel availability and storage
Electric hammer mills offer greater flexibility in installation and use, making them suitable for a wider range of applications.
Initial Investment
While initial costs can vary:
- Electric Hammer Mills:
- Generally lower upfront costs
- Simpler installation process
- May require electrical infrastructure upgrades
- Diesel Hammer Mills:
- Higher initial purchase cost
- More complex installation including fuel storage systems
- No additional infrastructure needed if fuel is readily available
Although electric models may require electrical upgrades, their lower initial cost and simpler installation often make them more economical.
Safety Considerations
Safety is a critical factor:
- Electric Hammer Mills:
- No fuel storage risks
- Lower fire hazard
- Safer in enclosed spaces
- Diesel Hammer Mills:
- Risks associated with fuel storage and handling
- Higher fire risk due to combustible fuel
- Emissions pose health risks in enclosed spaces
The safety advantages of electric hammer mills are significant, especially for indoor operations.
Conclusion
While both electric and diesel wood pellet hammer mills have their place in the industry, electric models generally offer superior benefits. They provide higher energy efficiency, lower operational costs, reduced environmental impact, easier maintenance, more consistent performance, greater versatility, and enhanced safety features.
The advantages of electric hammer mills align well with current trends towards sustainability, cost-effectiveness, and operational efficiency in the biomass processing industry.
For businesses considering investing in a wood pellet hammer mill, the electric option is often the better choice. It offers a more sustainable, efficient, and cost-effective solution for long-term operation. As the industry continues to evolve, the benefits of electric hammer mills are likely to become even more pronounced, solidifying their position as the preferred choice in wood pellet production.
For details please contact: Richi manufacture
WhatsApp:86 138 3838 9622
Email:enquiry@richipelletmachine.com