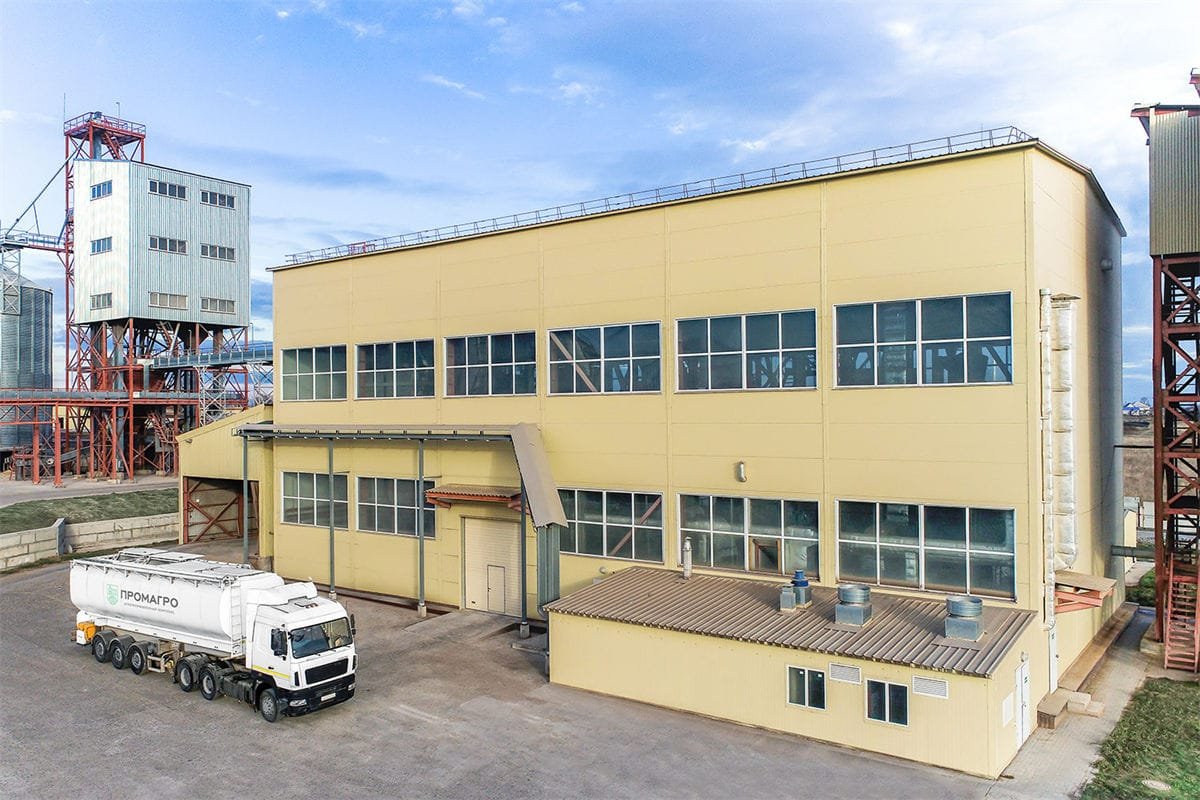
The aquaculture industry is expanding rapidly, driving a surge in demand for premium fish feed. As fish farming operations grow and consumers become more mindful of sustainable and nutritious seafood, the need for effective and reliable fish feed production facilities has increased significantly.
India, with its extensive coastlines, abundant freshwater resources, and burgeoning aquaculture sector, is an ideal location for setting up advanced fish feed production lines. These facilities can cater to both domestic and global markets, fulfilling the rising demand for high-quality fish feed products.
This comprehensive guide outlines the process of constructing an 8-30 T/H (tons per hour) fish feed production line in India, covering all aspects from feasibility studies and facility design to equipment procurement and operational considerations.
Step 1: Conducting a Feasibility Study and Market Analysis
Before initiating the construction of a fish feed production line, it is essential to conduct a thorough feasibility study and market analysis. This step will help evaluate the project’s viability, identify potential challenges, and develop a robust business plan.
The feasibility study should address several key areas:
- Market Demand Analysis: Assess the current and future demand for fish feed in India and neighboring regions, considering factors such as aquaculture production, species-specific needs, and consumer preferences.
- Raw Material Availability: Determine the availability and cost of essential raw materials like grains, proteins, vitamins, and minerals. Identify reliable suppliers and establish supply chain logistics.
- Site Selection: Choose appropriate locations for the facility, considering proximity to raw material sources, transportation infrastructure, utilities, and environmental regulations.
- Financial Projections: Create detailed financial projections, including capital investment requirements, operational costs, revenue forecasts, and potential return on investment (ROI).
- Regulatory and Legal Considerations: Understand local, state, and federal regulations governing fish feed production, environmental compliance, and food safety standards.
Market analysis should provide insights into the competitive landscape, consumer preferences, and potential market opportunities for your fish feed production line.
Step 2: Facility Design and Construction
With the feasibility study and market analysis complete, the next step is designing and constructing the fish feed production facility. This involves working with experienced architects, engineers, and aquaculture experts to develop an efficient design that meets production requirements.
Key considerations for facility design include:
- Production Layout: Optimize the layout to ensure efficient material flow, minimize waste, and maximize productivity, with dedicated areas for raw material storage, processing, packaging, and quality control.
- Equipment Integration: Design the facility to accommodate the integration of specialized fish feed production equipment, such as grinders, mixers, extruders, and dryers, ensuring optimal performance and ease of maintenance.
- Utilities and Services: Incorporate provisions for adequate power supply, water treatment, waste management, and other essential services.
- Environmental Considerations: Prioritize sustainability by incorporating features such as waste heat recovery systems, efficient water management, and proper waste disposal.
- Scalability and Future Expansion: Design the facility to allow for future expansion or modifications to accommodate increasing production demands or new product lines.
Once the design is finalized, the construction phase can begin, including site preparation, building construction, and the installation of necessary infrastructure and utilities.
Step 3: Procurement and Installation of Equipment
The core of any fish feed production line is the specialized equipment needed to process raw materials into high-quality feed products. This includes:
- Raw Material Handling and Storage: Efficient systems for receiving, storing, and transferring raw materials are crucial for smooth operations.
- Grinding and Mixing Equipment: High-performance grinders and mixers are essential for achieving the desired particle size and homogeneous blending of raw materials.
- Extrusion and Drying Systems: Extruders and dryers transform the raw material mixture into pellets or flakes, ensuring the desired moisture content and nutrient preservation.
- Cooling and Packaging Equipment: Efficient cooling systems and automated packaging lines maintain product quality and ensure efficient distribution.
- Quality Control and Monitoring Systems: Advanced quality control and monitoring systems, including laboratory equipment and data acquisition systems, ensure consistent product quality and compliance with industry standards.
Work closely with reputable equipment manufacturers and suppliers to ensure proper commissioning, calibration, and operator training.
Step 4: Operational Considerations and Workforce Development
Once the facility is constructed and equipped, focus on operational considerations and workforce development, including:
- Standard Operating Procedures (SOPs): Develop comprehensive SOPs for all aspects of fish feed production, including raw material handling, processing, quality control, and maintenance.
- Workforce Training: Invest in training programs for operators, technicians, and supervisors to ensure safe and efficient operations.
- Supply Chain Management: Establish robust supply chain management systems for sourcing raw materials, distributing finished products, and managing inventory levels.
- Regulatory Compliance: Ensure compliance with all relevant regulations, including food safety, environmental, and labor laws.
- Maintenance and Contingency Planning: Implement preventive maintenance programs and develop contingency plans for potential equipment breakdowns, power outages, or other emergencies to minimize downtime.
Step 5: Quality Assurance and Product Development
In a competitive fish feed market, quality assurance and product development are essential for establishing a strong brand reputation and maintaining customer loyalty. This involves:
- Quality Control Protocols: Implement rigorous quality control protocols at every production stage to ensure consistent quality and compliance with industry standards.
- Nutrient Analysis and Formulation: Conduct regular nutrient analysis and optimize feed formulations to meet the specific nutritional requirements of various fish species and life stages.
- Product Innovation: Invest in research and development to explore new feed formulations, alternative protein sources, and innovative processing techniques that enhance product quality, nutritional value, and sustainability.
- Certifications and Accreditations: Pursue relevant certifications and accreditations to enhance the credibility and marketability of your fish feed products.
- Customer Feedback and Continuous Improvement: Establish channels for customer feedback and implement continuous improvement processes to address issues and enhance product quality and customer satisfaction.
By prioritizing quality assurance and product development, your fish feed production line can establish a strong competitive edge, fostering customer loyalty and positioning itself as a leader in the Indian and global aquaculture markets.
Building an 8-30 T/H fish feed production line in India is a complex and multifaceted endeavor requiring careful planning, execution, and commitment to excellence. By following these steps and adhering to industry best practices, aquaculture businesses and entrepreneurs can create a thriving and sustainable venture that contributes to the growth of the Indian aquaculture industry while meeting the ever-increasing demand for high-quality fish feed products.
Success lies in continuous innovation, collaboration, and a relentless pursuit of quality and sustainability. By embracing cutting-edge technologies, prioritizing environmental stewardship, and fostering a skilled and dedicated workforce, your fish feed pellet production line can pave the way for a more sustainable and resilient future for the Indian aquaculture sector, ensuring a secure and abundant supply of nutritious seafood for generations to come.